Rotating Detonation Engines
The UCF Rotating Detonation Rocket Engine (RDRE) was modeled after the Air Force Research Laboratory’s Dist. A. RDRE at Edwards Air Force Base. Early stages of testing focused on experimentally identifying an operational regime for gaseous hydrocarbons and oxygen. Testing capabilities have enabled a design framework to iteratively design, test, and evaluate injectors based on propellant selection and mission objectives. This project has validated the detonability of gaseous hydrogen and oxygen. Current emphasis is placed on studying the stability limits for H2/O2. These efforts are intended to inform a larger design framework for RDRE architecture and its technology readiness level.
Investigate affects of seeded carbon black particles on detonation wave speeds and CTAP pressures in an H2-Air RDE. The effects of various biofuel particles i.e. (peanut flour, powdered sugar, and cornstarch powders) are also investigated. Push operability limits of RDE based on saturation of particles seeded in the flow (fuel/air equivalence).
The UCF Rotating Detonation Rocket Engine (RDRE) was modeled after the Air Force Research Laboratory’s Dist. A. RDRE at Edwards Air Force Base. Early stages of testing focused on experimentally identifying an operational regime for gaseous hydrocarbons and oxygen. Testing capabilities have enabled a design framework to iteratively design, test, and evaluate injectors based on propellant selection and mission objectives. This project has validated the detonability of gaseous hydrogen and oxygen. Current emphasis is placed on studying the stability limits for H2/O2. These efforts are intended to inform a larger design framework for RDRE architecture and its technology readiness level.
A linear RDRE with the same dimensions and injectors as the regular RDRE was designed and built for the purpose of studying the detonation structure and the interactions between reflected shock waves and fresh reactants. This is performed in an attempt to gain understanding on how mode transitions occur in a regular RDRE. This configuration allows for important diagnostic techniques to be used such as particle image velocimetry (PIV), chemiluminescence and schlieren imaging.
Hypersonics
Hypersonic vehicles are not only limited by our current state-of-the-art propulsion systems, but also by conventional materials. At Mach 5 speeds and greater, sections of the vehicle can face as much as 3000 degrees Kelvin. Understanding how novel materials can stress, deform, and survive in these extreme temperatures is the key step to integrating these new materials into our future hypersonic vehicles. Paired with advanced manufacturing techniques, HYPERMAN seeks to bridge the gap between material composition (plus fabrication) and the high-speed reacting flows of hypersonic technology.
In a joint venture with Penn State and Purdue, the goal of this project is to incorporate solid fuels in hypersonic applications. Utilizing cutting edge solid fuels created with novel manufacturing methods, we will design a facility to simulate flight up to Mach 6, paving the way for air-breathing hypersonic vehicles. Solid fuels are desirable over liquid and gaseous fuels due to their simplicity and are used in many applications, from missiles to solid rocket boosters for space propulsion
Scramjets can achieve speeds above five times the speed of sound. This is possible through shock compression of air and fuel paired with supersonic combustion. However, initiating a supersonic engine is more complex than a conventional spark ignition system in our modern-day passenger airplane engines. It is akin to lighting a match in a tornado: any effort to initiate combustion will be snuffed out by the high-speed flow. Current mechanisms to assist initiation involve geometric cavities and bluff-bodies. The scramjet igniter project seeks to explore alternative methods to generate high pressure and high activation energy with liquid fuels.
Axial - Stage Combustion Chamber
As the world becomes more aware of the effects of global warming/climate change on the planet, the demand for different tools and mitigation strategies grows exponentially. One of the many strategies proposed is Stratospheric Aerosol Injection, or the injection/creation of several different aerosols in the stratospheric region of the atmosphere. Several injection concepts exist, but direct injection of the initial fluid into the vitiated plume of an aircraft engine shows the most promise. The purpose of this project is to characterize several injection concepts and their resulting development into an aerosol in the plume of the facility.
The emission of NOx in current gas turbine systems is a primary concern for design and operation and is a constraint on combustor efficiency. One method for reducing NOx emissions and increasing the turbine inlet temperature involves axially staging in the combustor. This process involves separating the combustion into multiple stages in which a lean mixture is burned in the headend stage and additional fuel is introduced downstream to raise the combustor product exit temperature. By reducing the time the combustion products are at the exit temperature, NOx formation can be limited. The interaction of the flame and flow fields have been studied along with emission measurements to understand the impact of varying axial conditions.
Greater restrictions on allowable emissions have pushed industry towards reducing the output of CO2 and NOx, with an ultimate goal of net-zero carbon emissions by 2050 in the US. One way to progress toward this goal in current industrial systems is by converting from natural gas to hydrogen as the primary fuel source. However, this transition requires careful study due to the highly reactive nature of hydrogen-air mixtures. This project aims to investigate the flame behavior of methane-hydrogen fuel blends in order to anticipate changes in stability and position. Due to the higher burning velocity of hydrogen, flashback is a primary concern because of the damage it can cause to the combustor flame holder and walls.
Ramjet / Afterburner
The research experimentally investigates the role of inlet turbulence and mean pressure gradients on the reacting flow dynamics in a premixed bluff-body combustor. The experimental facility incorporates a high-speed ramjet combustor with a bluff-body flameholder. The inlet turbulence conditions are controlled with a dynamic turbulence generator upstream of the combustor, while the streamwise pressure gradient is altered by modulating the combustor wall geometry into a converging nozzle, a straight nominal section, or a diverging diffuser. High-speed particle image velocimetry (10-20 kHz) and chemiluminescence imaging (10 kHz) are used to obtain time-resolved velocity fields and flame topologies. To quantify turbulent flame-vertex dynamics, the analysis relies on the vorticity transport equation to identify the key mechanisms that control the behavior of the reacting flow. The methodology relies on a Lagrangian-based fluid element tracking method to quantify vorticity transport across the premixed flame. The results demonstrate that vorticity transport is augmented as the magnitude of the pressure gradient is increased; however, the vorticity balance is more sensitive to turbulence effects. At low inlet turbulence conditions, both flame and flow dynamics are controlled by flame-generated baroclinic torque. However, at high turbulence conditions, the flame and flow field are primarily controlled the stretching and bending of vortices.
There remains a need to improve energy conversion efficiencies and minimize the environmental impacts of combustion systems. Operating at lean premixed conditions significantly improves efficiency, reduces thermal losses, and limits NOx emissions. However, lean flames are susceptible to static and dynamic instabilities, which may result in local flame extinction or complete blowout in which the reaction is terminated in the combustor. Thus, the research explores the temporal extinction dynamics of a premixed bluff-body flame. The investigation leverages a high-speed premixed ramjet combustor with a bluff-body flameholder. Measurements are obtained using a suite of high-speed laser and optical diagnostics including: (1) a wide-field, two-component particle image velocimetry (PIV) system, (2) a high-resolution, three-component stereoscopic PIV system, and (3) a line-of-sight C2*/CH* chemiluminescence imaging system. The diagnostics allow for the instantaneous flow field, flame structure, local flame strain rates, and equivalence ratio to be simultaneously measured during the lean blowout transient. The results detail the mechanisms leading to flame extinction, which primarily consist of flame and shear layer interactions near the reattachment point in the bluff-body wake. Additionally, the role of inlet flow velocity, inlet turbulence conditions, and mean pressure gradients are all explored to provide a comprehensive understanding of lean blowout in propulsion and energy combustion systems.
Turbulent Shock Tube
Deflagration to detonation transition is a complex phenomena with applications in hypersonic engine development, explosion safety, and interstellar combustion. The research at PERL seeks to advance knowledge in this community through examining the conditions need to initiate a detonation with a combination of planar and line-of sight diagnostics. Through these measurements, a greater understanding of the flow conditions required for detonation onset is attained. Additionally, the research offers insight into flame-turbulence interaction physics and potential mechanisms for onset. Once a detonation is initiated the research seeks to quantify the frontal physics and cellular structure of detonation propagation. Subsections of this research consists of ramp initiated detonation onset, ignition and propagation properties at different Lewis numbers and unconfined detonation propagation.
High-speed air-breathing propulsion systems (Gas turbine engines, afterburners, ramjets and scramjets) relay on turbulent combustion for thrust generation. A turbulent flame stabilization mechanism is required to sustain a flame in the high velocity streams within these engines. Although this approach for flame stabilization is effective, combustion stability (static and dynamic) limits improvements in combustion efficiency and emission reduction due to flow field complexities. Furthermore, combustion instabilities are detrimental to efficiency and cause fatigue to system components. The research is focused on understanding the physical mechanisms influencing static and dynamic combustion stability to improve development of efficient combustion systems and reduce pollutant emissions (NOx, CO, soot).
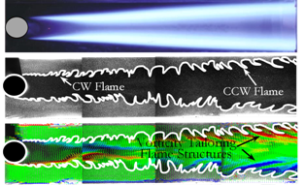
The research is formulated a physics-based model using key fundamental physical mechanisms for flame extinction. The novelty of the model is that it interactively couples the physics of the turbulent flow through a dynamic Lagrangian vortex element method and the strained flame reaction kinetics using a opposed-jet flame for the reaction kinetics. This novel modeling strategy would effectively capture the dynamic flame stability and extinction for turbulent premixed combustion resulting in the proliferation of innovative solutions for turbulent combustion-reliant systems for increased efficiency, broadened safe operating domain, and reduced emission of harmful pollutants.
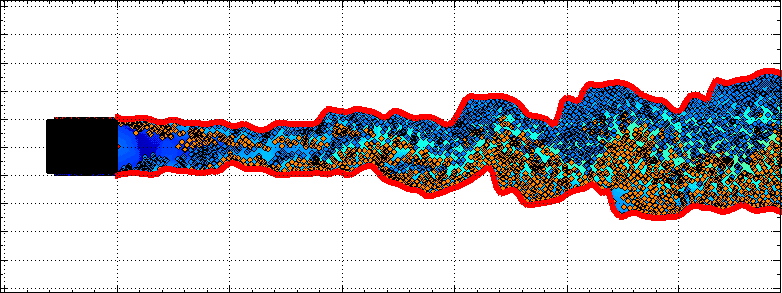
Pressure gain combustion, in the form of detonation, is an innovative scheme of turbulent combustion that increases combustion system efficiencies. The fundamental mechanism for achieving detonation is turbulent flame acceleration from deflagration-to-detonation. The process involves generation of high flow turbulence intensities and length scales for effective flame acceleration and propagation. The objective of the work is to investigate the fundamental physics of deflagrated flame dynamic interaction with the fluidic jet flow. The research will institute an understanding for the mechanisms of transient turbulent interaction structures, vortex dynamics, shear layer instabilities and jet instability modes.
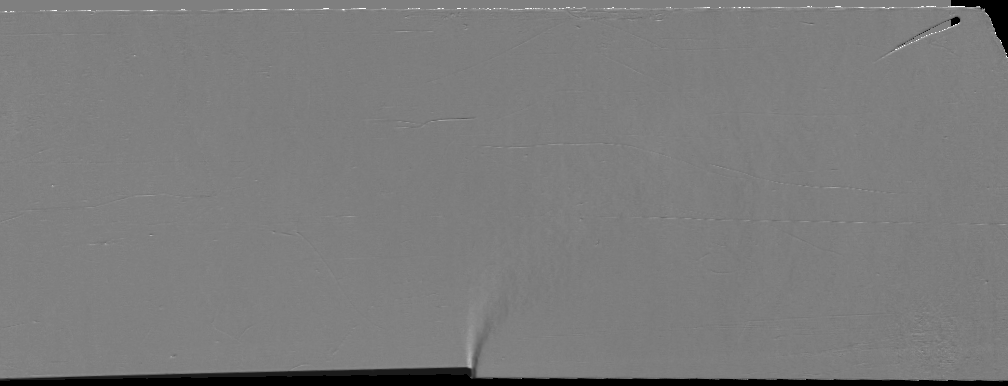
A jet in crossflow is a conventional approach for fluidic flow control. The research studies the fluidic-flow interaction and vortex dynamics in terms of temporal formation, evolution and instability for jets in crossflow. The research characterizes the jet interaction with the crossflow and investigates the fundamental mechanisms driving shear layer interaction and turbulent flow structures.

The objective of this study was to develop an advanced 3D tomographic optical diagnostic technique of flames. This was accomplished using light-field reconstruction of images taken of a premixed jet flame. This was accomplished using light-field reconstruction of images taken of a premixed jet flame. Development of a novel system for visualizing the intensity regions of flames will improve study combustion efficiency of flames. A model was developed for 3D tomographic imaging and used to investigate and characterize flames. The program makes use of high-speed photography to capture images of different angles of the flame and reconstruct the full flame from the information gathered.
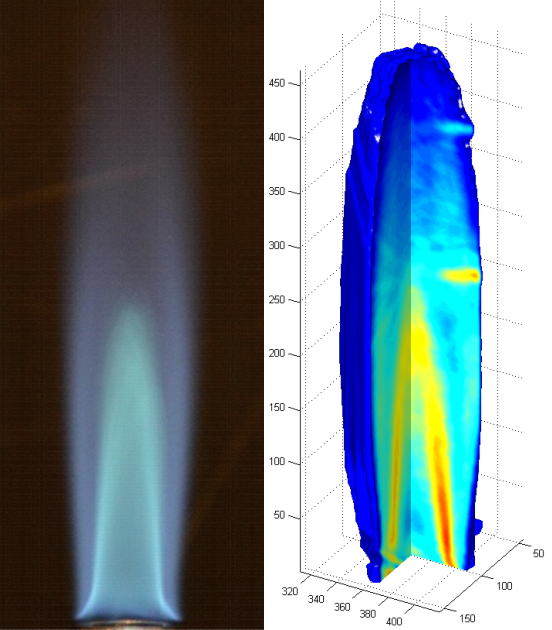
The study investigates under-expanded microjets fluidic-flow coupling in terms of flow physics of the shearlayers interaction and Mach wave interference. The research characterizes the interaction modes based on spatial proximity of the microjets and cultivates scaling models for the interaction modes.
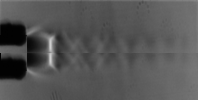
The research is investigating unsteady aeromechanic interactions and propulsion. Understanding unsteady aeromechanic interactions require time-resolved solutions and response to dynamic conditions to capture the flow physics. A Lagrangian element vortex model formulated using key flow physics is used in parallel to 4D-PIV to understand the dynamics of the flow interaction physics and separation.
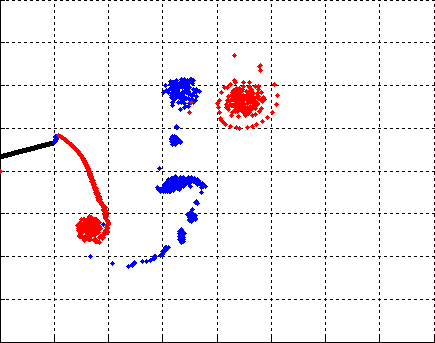
The sharp focus system measures true quasi-planar two-dimensional visualizations of refractive disturbances using light-field function. It is superior to line-of-sight Schlieren and shadowgraph visualization. Furthermore, velocity field measurements are attained from particles (PIV) and reacting or nonreacting flow structures. The system is unique in that it provides PIV measurements at extreme sampling rates (>50kHz) relative to traditional PIV systems.
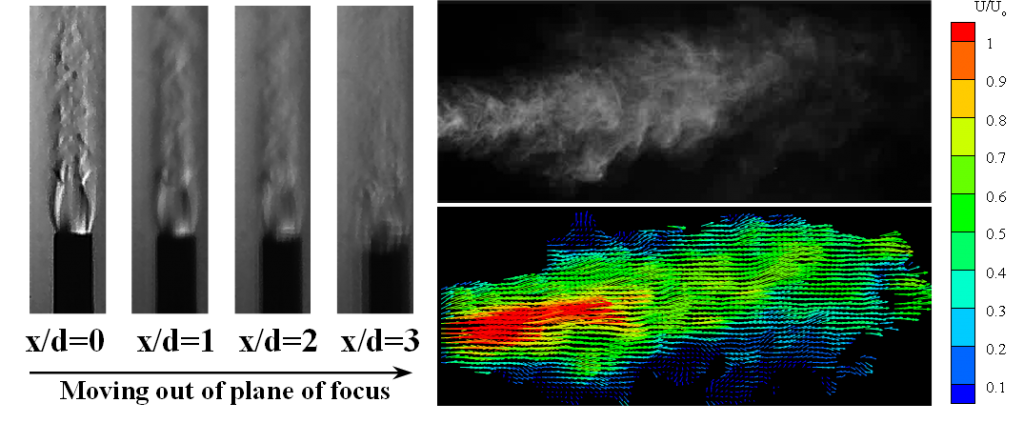