One year before the first human set foot on the Moon, Florida Technological University opened its doors just 35 miles west of NASA’s Kennedy Space Center (KSC) on Florida’s Space Coast. The university was created by the Florida State Legislature with the mission of training personnel to support the rapidly growing space program at KSC. By 1978, the university had expanded its academic scope beyond engineering and technology, so Florida Tech was rebranded as the University of Central Florida (UCF). Even so, the university remained in close partnership with NASA over the decades.
The retirement of the space shuttle fleet had tremendous repercussions on the Space Coast economy, causing a mass exodus of engineering talent from the area. As the dust settled, NASA forged a path forward with private space companies aiming to develop reliable rockets to resupply the International Space Station, launch satellites, and even offer spaceflights to private citizens. Burgeoning startups like Elon Musk’s SpaceX, Jeff Bezos’ Blue Origin, and Richard Branson’s Virgin Galactic were vying for their positions in the new, privatized space race and set up offices around KSC. Although this brought some skilled labor back to the area, these startups were operating on lean capital compared to the vast crews working on the shuttle program. Established aerospace companies like Raytheon, Lockheed Martin, and Northrop Grumman already had a presence in the area, and as the startups grew, UCF continued supplying talent. Today, UCF, one of 52 space-grant universities throughout the U.S. and Puerto Rico, boasts that almost a third of all KSC employees are UCF alumni, and countless other alumni work for area companies supporting the U.S. space industry.
Besides remaining a talent supply chain hub, UCF’s Department of Mechanical and Aerospace Engineering has also worked closely with KSC over the years developing new technologies. Jihua ‘Jan’ Gou, Ph.D., founded the Composite Materials and Structures Laboratory at UCF in 2007 and has worked on several composites and coatings projects funded through KSC and the Florida Space Grant Consortium. Over the past 20 years, Gou has been exploring research on structural composites (polymer matrix composites and ceramic matrix composites) and polymer nanocomposite coatings for flame retardancy, hydrophobicity, abrasion resistance, antimicrobial features, electromagnetic interference (EMI) shielding, lightning strike protection, and thermal protection. Gou reflects, “For most of my academic life, I have been thinking of how to replace traditional materials like steel, alloy, aluminum, plastics, and concrete with various types of composite materials for engineering systems such as spacecraft, aircraft, cars, machinery, and infrastructure.” Gou pauses and then adds, “Sometimes our ideas have worked. But some ideas didn’t work well so we had to seek a compromised solution using coatings, which brought me to this fascinating field.” In addition to his work with composites, Gou has been working to advance a high- performance polyimide powder coating originally developed by NASA’s Scott Jolley in 2014.
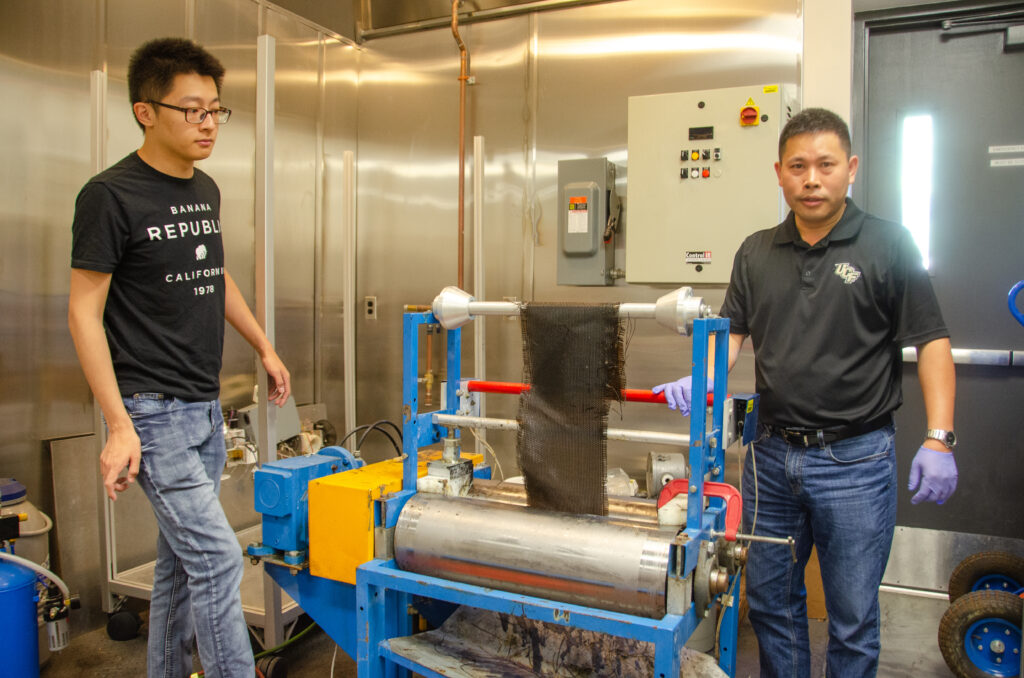
Powder Coating: Low Cure, High Heat Resistance
The high-performance polyimide powder coating NASA and UCF have been developing is based on the polyamic acid (PAA) polymer, which has a low melting point in the range of 75-100 degrees Celsius (167-212 degrees Fahrenheit). According to Gou, one of the secrets behind this potentially revolutionary technology is controlling the molecular weight, or the sum of the atomic weight values of the atoms in a molecule. “If you control the molecular weight, you control the melting point,” instructs Gou. Additionally, the chemical end-caps used at the extremities of polymer chains are useful for grafting to and from a polymer chain, says Gou, and are important in determining the properties and potential applications of the polymers.
The process of applying the PAA powder should sound familiar to powder coaters. The substrate is heated to 75-100 degrees Celsius (167-212 degrees Fahrenheit) so as the powder is applied it can melt and flow into a smooth coating on the substrate. The PAA powder is applied to the substrate using traditional electrostatic powder coating techniques. After application, the coated substrate is further heated to 200 degrees Celsius (392 degrees Fahrenheit) to promote crosslinking, and the PAA polymer cures to the polyimide coating. Therefore, this type of coating can be obtained at a lower processing temperature of 200 degrees Celsius (392 degrees Fahrenheit). However, conventional high temperature resins such as Teflon, nylon, and polyimide have high melting points of >200 degrees Celsius (392 degrees Fahrenheit) and high viscosities.
Salt spray testing was conducted at KSC to determine corrosion resistance. Polyimide-coated steel and aluminum panels were exposed to sodium chloride for 1,000 hours at 35 degrees Celsius (95 degrees Fahrenheit), in comparison with panels coated with epoxies, polyesters, and epoxy-polyester hybrids. The rust grade on these panels was evaluated using the ASTM B-117 rating method. Based on the initial results of evaluations, the polyimide coating performed as well as or superior to commercial-grade powder coatings.
Gou says this technology does not contain any materials listed under Prop 65, but its qualifications related to TGIC and food and water contact have not yet been investigated. He believes the PAA powder has potential use as 3D printing filaments and fiber-reinforced composites with carbon fiber, glass fibers, etc. Other potential applications include multi- functional materials for high temperature applications if nanomaterials are dispersed into the PAA powders. However,Gou cautions the chemistry of the PAA polymer powder still needs to be optimized in order to tailor it to specific applications. In addition, more R&D work is needed for scaling up of the process.
Because of the promise Gou has seen with this new technology, he is actively seeking partners to advance testing with the end goal of commercialization. He believes there are applications for use in automobiles, aircraft, spaceships, and even marine environments. Gou explains that when technologies are initially developed through government agencies such as NASA, projects are typically funded for only two to three years, and then commercial partners are sought to explore and develop the research further. He says unfortunately there is often a time gap before a private company picks up the research and begins to develop it into a proven technology, which can significantly delay refinement of critical emerging technologies. The upside, he says, is that private sector companies are often more efficient with the R&D process, placing appropriate restrictions on time and resources once they are engaged. “It won’t work without good industry partners, because industry partners know the needs of end-use customers such as product requirements, industry standards, and profitability,” says Gou.
Numerous studies have been done over the decades that show the immense positive economic impact PPP have had on the U.S. economy. The 2017 Economic Impact Report prepared by NASA for their Small Business Innovation Research (SBIR) and Small Business Technology Transfer (STTR) awards found that for Fiscal Year 2016, these programs created 2,412 jobs, $474 million in economic output, and $57.3 million in fiscal impact with an initial investment of $172.9 million. Perhaps this new powder coating technology will be developed into a viable product and factored into future economic impact reports.